Industrial Furnace
Walking Beam Type Heating Furnace
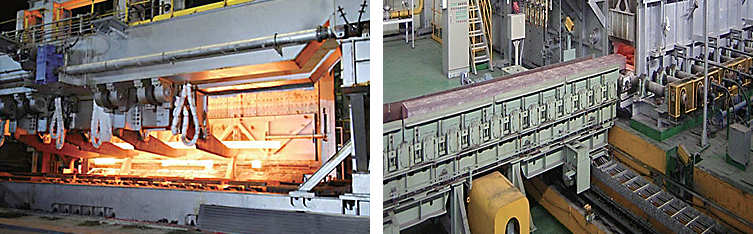
Application
- Furnace type : Walking beam, Pusher type
- Treatment material : Copper, Copper-Alloy Slab
Features
- Capacity : Max 100Ton/hr
- Temperature : Max 1,100℃
- Heating source : Gas, Oil
Advantages
- Furnace temperature control facilities
- Production of high quality products
- Energy saving
- Full automatic system
- High productivity
- Material Temperature uniformity
- High durability
Mesh Belt Type Heat Treatment Furnace
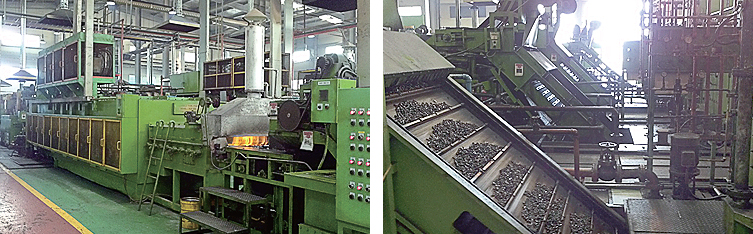
Application
- Carburizing, Quenching & Tempering and
Heat-treatment - Treatment material :
Automobile parts, Fastener etc.
Features
- Capacity : Max 1.5Ton/hr
- Temperature : Max 950 ℃
- Atmospheric Gas : Rx-gas, Methanol
Advantages
- High quality of heat treatment
- Full automation system
- Maintenance cost down
- Uniformed temperature
Mg SOF
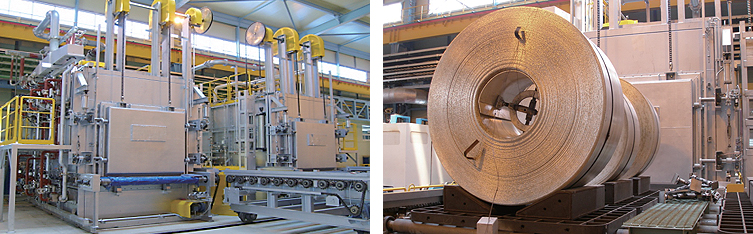
Application
- Furnace type : Mg soaking
- Treatment material : Mg strip coil
Features
- Capacity : Max 30Ton/ch
- Temperature : Max 600℃
- Heating source : Gas, Heater
- Atmosphere gas : N2 gas
Advantages
- Material temperature Uniformity
- Production of high quality products
- More energy saving
- Quality improvement
- High productivity
- Full automatic system
Low Pressure Carburizing (GQ/OQ)
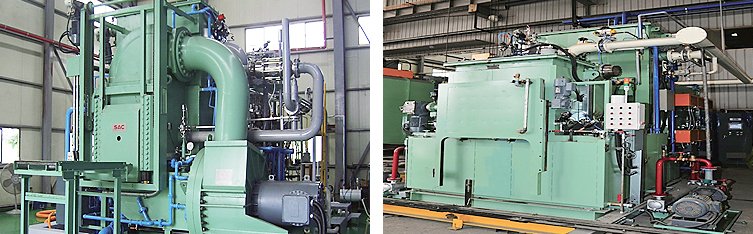
Application
- Mass Production for auto
motive gear and shaft
Features
- Carburizing Temp : 850 ~ 1,050℃
- Carburizing Pressure : 1 ~ 30mbar
- Carburizing Time : 5min ~ 5hr
- Carburizing Depth : 0.3 ~ 3mm
- Gas Quenching : Max 20bar (N2, He)
Advantages
- Production of high quality products
- Environmental Protection, non-pollution
- Shortens process time and reduce costs of 35%
- Fully automatic system
- Reducing the Processing time of 30~50%